Robot Vision by EVT
Key Features
Simple und intuitiv
Hand-eye calibration for robots and handling systems
No programming knowledge required
Thanks to the drag and drop feature of the EyeVision software
2D and 3D Object recognition
Thanks to 3D point cloud evaluation
Bin Picking
Recognition of the position and shape of each object Finding and picking out unsorted parts in a box
Palettizing and Depalletizing
Detection of objects through deep learning Fast, precise and autonomous actions
Object Sorting
Precise recognition of the position and shape of objects Sorting out incorrect or faulty objects
Pick and place
Localizing and picking object at high speeds
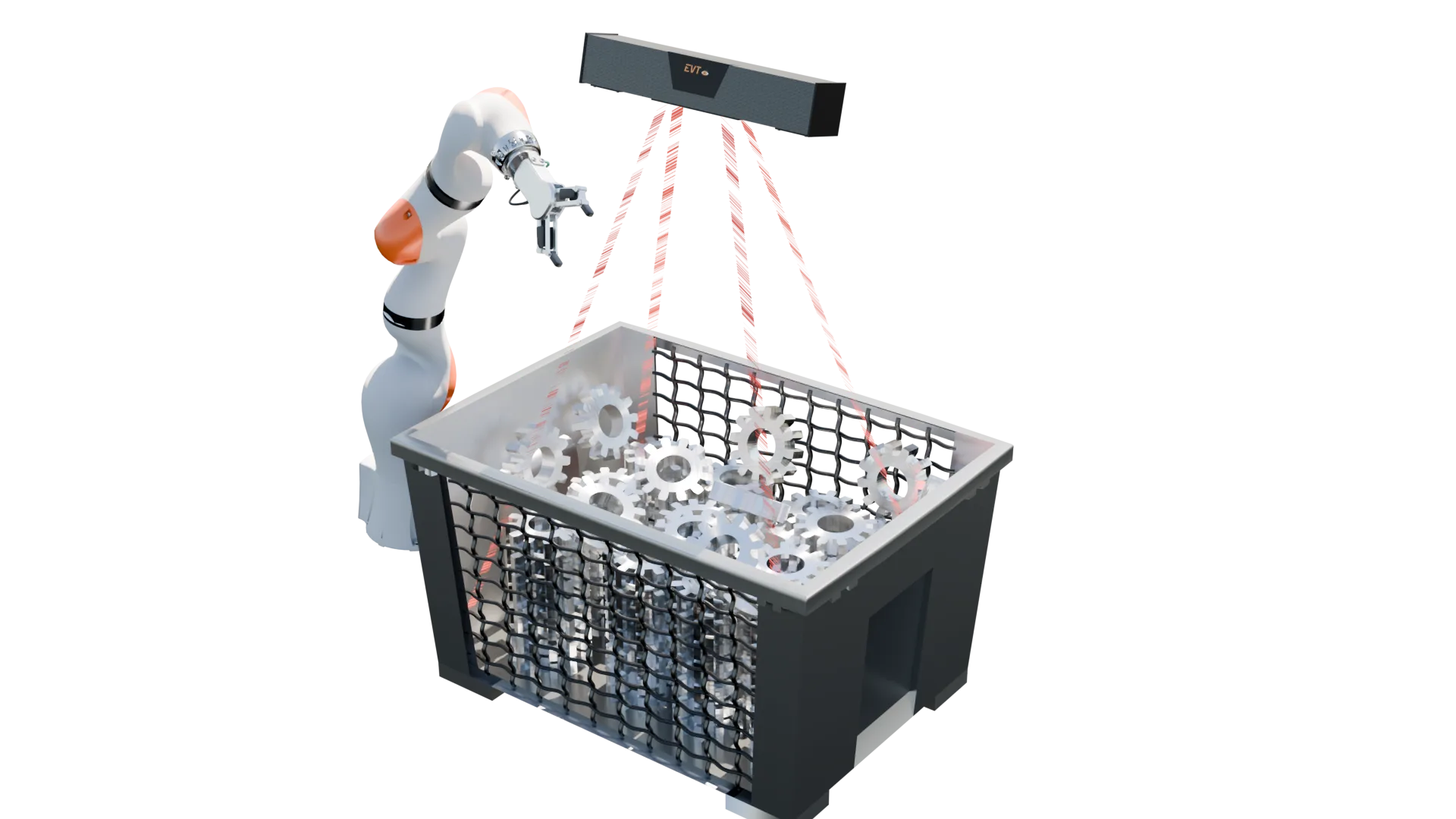
Bin picking is an automated technology in which robots remove objects from bins that have been placed out of order. 3D sensors are used to detect the exact position of the objects in the room and transmit this to the robot. This method is ideal if the objects are not pre-sorted and are available in any orientation.
Sensor
3D sensors for depth detection
Objects position
Disordered, random positions and orientations
Complexity and challenges
Recognize overlapping, twisted or difficult to grasp objects requires 3D detection and collision avoidance -> high complexity
Palletizing and depalletizing with Robot Vision enables the automatic stacking and removal of goods using intelligent image processing. By using 2D or 3D cameras, robots recognize the position, orientation and shape of objects, enabling precise handling without manual intervention. This technology increases efficiency in logistics and production by speeding up work processes and reducing errors.
Sensor
2D/3D cameras for object recognition and orientation
Objects position
Mostly ordered on pallets
Complexity and challenges
Ensure stability of stacked objects - requires precise stacking/removal positions
Object sorting with Robot Vision enables automated detection, classification and sorting of objects based on characteristics such as shape, color, size or codes. By using 2D or 3D cameras, the system records the relevant properties and forwards the objects to the correct position. This technology increases efficiency in production and logistics, reduces errors and minimizes manual effort.
Sensor
2D/3D cameras for classification
Objects position
Ordered or unordered, but classifiable
Complexity and challenges
Correctly distinguish similar objectsr - equires classification according to certain features -> trainable with Ai
Pick-and-place with Robot Vision enables the precise picking and placing of objects by robots equipped with intelligent image processing systems. 2D cameras record the position, orientation and properties of the objects and transmit this information to the robot. This allows components, workpieces or products to be moved efficiently and error-free, which significantly improves automation in production, logistics and assembly.
Sensor
2D cameras for object recognition
Objects position
Mostly sorted or known
Complexity and challenges
Precise handling, different object shapes - requires precise detection of position
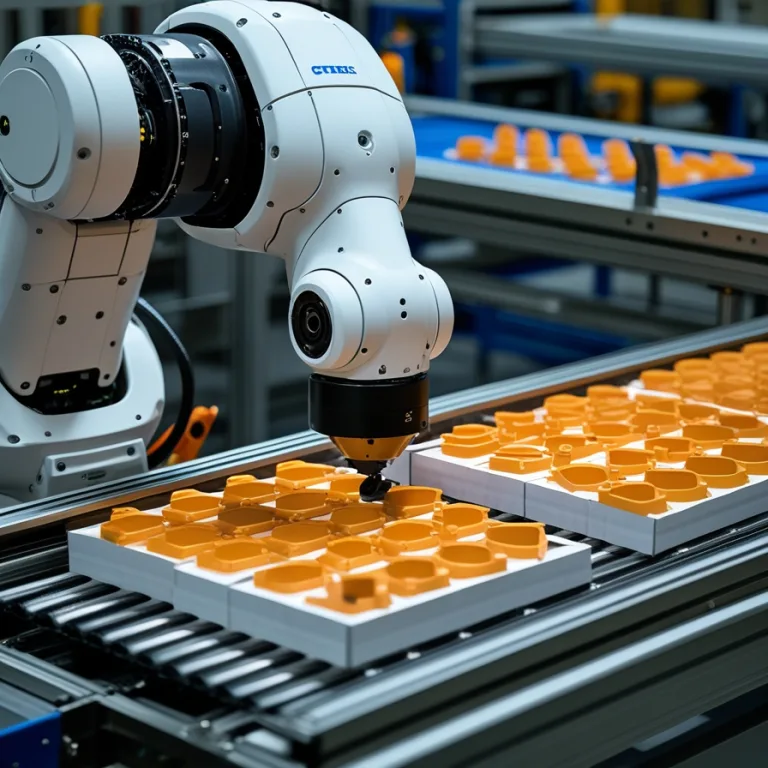
AI-driven object recognition within images
The EyeVision software efficient segmentation for detailed data extraction. Starting with image capturing and preprocessing it based on convolutional neural networks. Through advanced feature detection, we enable seamless data conversion, analysis, and interpretation. All of this is powered by our softwares versatile AI implementation, ensuring precision and adaptability across applications.
Efficient segmentation for detailed data extraction
Based on EVT versatile AI Implementation:
- Various pre trained Networks
- Easy to adapt through Transfer Learning
- Used for Detection and Segmentation
- Data Augmentation