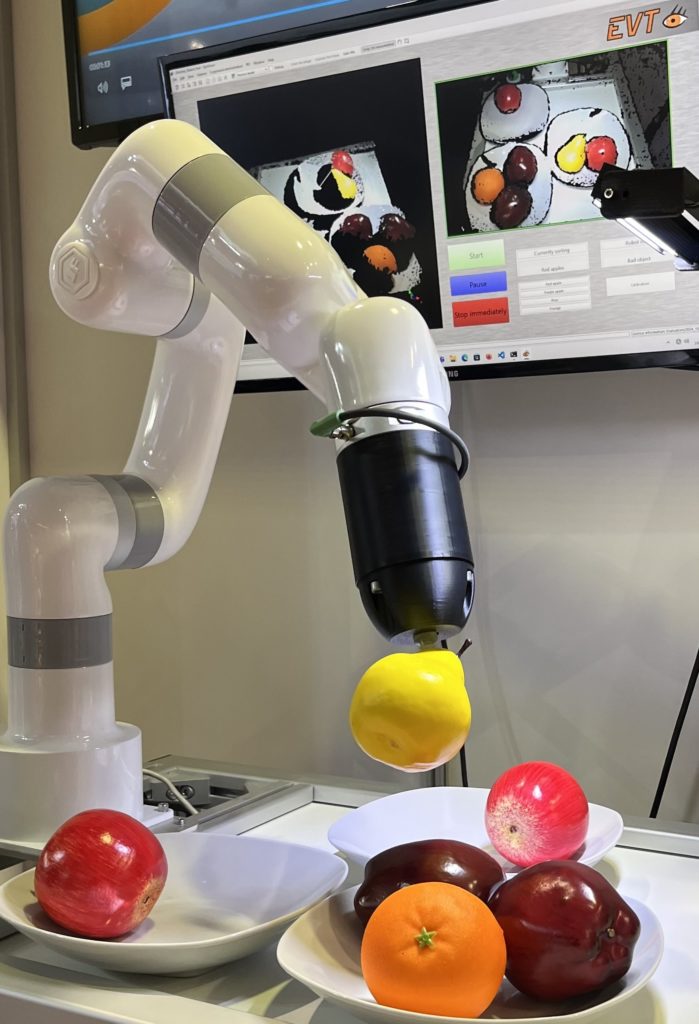
EyeVision by EVT is a powerful image processing software known for its flexibility and ease of use. It is hardware independent, giving you the freedom to choose the camera, computer or operating system that best suits your needs. This versatility makes EyeVision an ideal solution for image processing companies that need reliable software that seamlessly integrates with their existing systems.
In addition to classic applications such as line camera applications, 2D applications and 3D applications, EyeVision offers specialized modules that enable AI-based solutions and robotic applications. This opens up numerous possibilities for solving complex tasks in automation technology. EyeVision RV (Robot Vision) is specifically designed to solve robot vision tasks quickly and easily. Whether it’s a 2D or 3D task, the intuitive interface and powerful tools for hand-eye calibration and robot integration allow users to complete their projects efficiently.
An outstanding feature of EyeVision is the integrated hardware configurator, which allows you to connect a camera in no time at all. Tedious driver installations are a thing of the past and the camera can be connected to the software within minutes. This saves time and significantly reduces setup complexity. Application solutions can be implemented using standard algorithms or, for more complex challenges, enhanced with built-in AI technology. Even if a product hasn’t been detected before, the built-in transfer learning allows new products to be trained quickly and easily.
Another key aspect of using robots is merging the two local coordinate systems—the camera’s and the robot’s. This is critical for successful robotic applications. EyeVision integrates hand-eye calibration into a function tool that works at the push of a button, greatly simplifying the process and allowing users to focus on the core tasks.
EyeVision’s standardized robot interface further facilitates robot connectivity. This tool translates the vision results into a data format that can be read by the robot and sends it to the robot. In return, the robot’s data is prepared for use in image processing. If the robot is already trained, it is simply selected; if not, the user can easily add a new robot. If the robot supports ROS 2, this interface can be used without any problems.
In EyeVision’s view, Robot Vision encompasses all tasks where a robot needs a camera to perform its functions. This includes, for example, detecting parts on a conveyor belt or in a bin so that they can be picked up and either fed into a production step or placed in another location. Whether it’s a SCARA robot or a multi-axis system, the control commands can always be adapted.
EyeVision Robot Vision provides a variety of key features to increase the efficiency and accuracy of robotic applications:
- Simple, fast and intuitive hand-eye calibration: Calibration is quick and easy, reducing training time.
- Deep learning, AI-driven object detection and segmentation: These technologies enable accurate object recognition and processing.
- 2D and 3D object detection: The software can identify and process both flat and three-dimensional objects.
- Point cloud analysis: Particularly useful for complex 3D applications.
- Color recognition: The ability to recognize colors greatly expands the range of applications.
- Flexible robot integration: The software easily adapts to different robots and systems.
- No programming required thanks to drag and drop: This feature makes the software accessible to users without programming knowledge.
- Ability to achieve absolute accuracy: Specialized functions can be used to improve the accuracy of robotic applications beyond standard specifications.
To get started with EyeVision RV, simply connect the robot to the defined interface. Next, perform a hand-eye calibration to align the robot and camera in the same coordinate system. Once the robot and EyeVision are connected, the task parameters can be easily set up using drag-and-drop functionality.
If necessary, the robot’s axis play can be accounted for using EyeVision’s Absolute Accuracy feature, which further corrects the robot’s workspace. This allows the robot to operate with even greater precision than its specifications indicate. This process is also automatic – users only need to activate the required function tool.
Regardless of the production process—be it in the automotive, electronics, electrical engineering, food, or logistics industries—anywhere robots are used, they can work more flexibly with Robot Vision. Standard applications include palletizing, depalletizing, bin picking, and object sorting. Thanks to the high accuracy achieved through correction of robotic inaccuracies, EyeVision can also support highly precise assembly tasks in collaboration with robots. For example, it can place electronic components on circuit boards with micron-level accuracy.
Combining robotics and image processing has never been easier. EyeVision makes the integration of Robot Vision into your production processes not only easier but also more efficient and precise. The future of automation is here, and EyeVision is ready to support you on this journey.
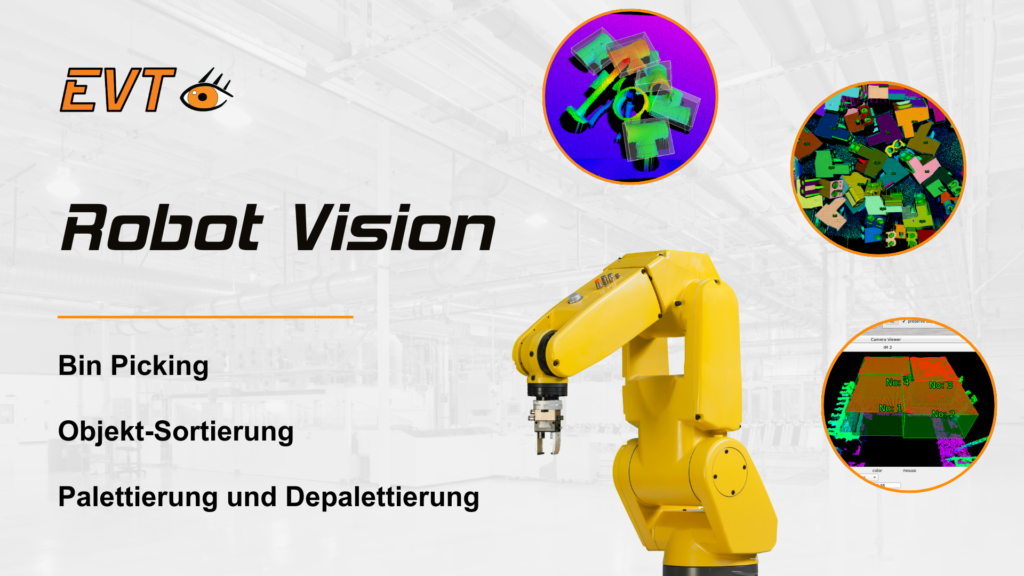