An intelligent system!
The EyeSorter is an intelligent system with adaptive parts flow control and optical workpiece identification.
It sorts small parts according to type, position orientation, quality and also according to piece count (piece count preselection).
Particularly in the case of high part rates and a large variety of types, it is suitable for trouble-free feeding of small parts to automatic assembly and production machines. Thus, defective parts can be reliably sorted out with the EyeSorter, the assembly of wrong types can be avoided and set-up times can be reduced to a minimum.
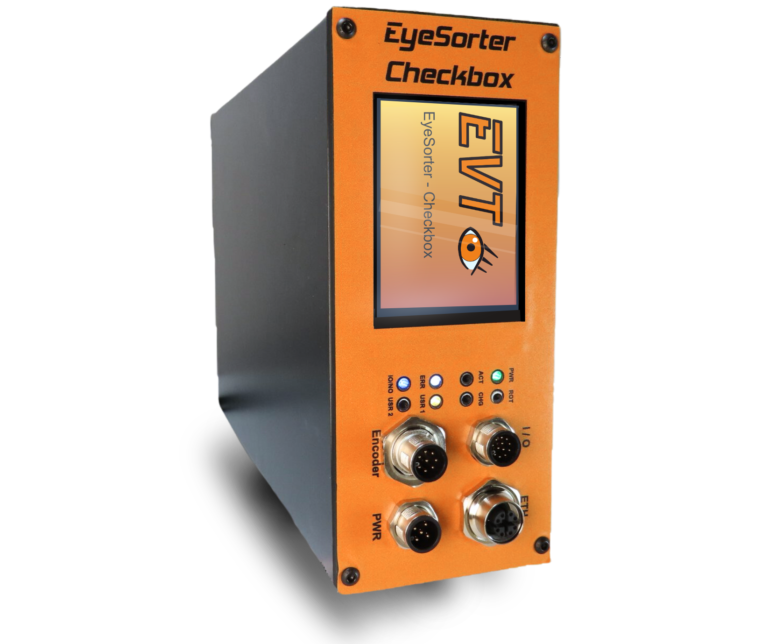
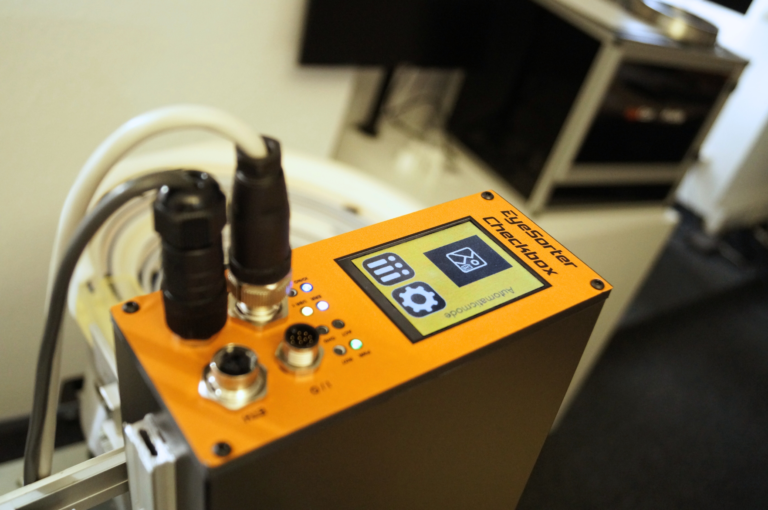
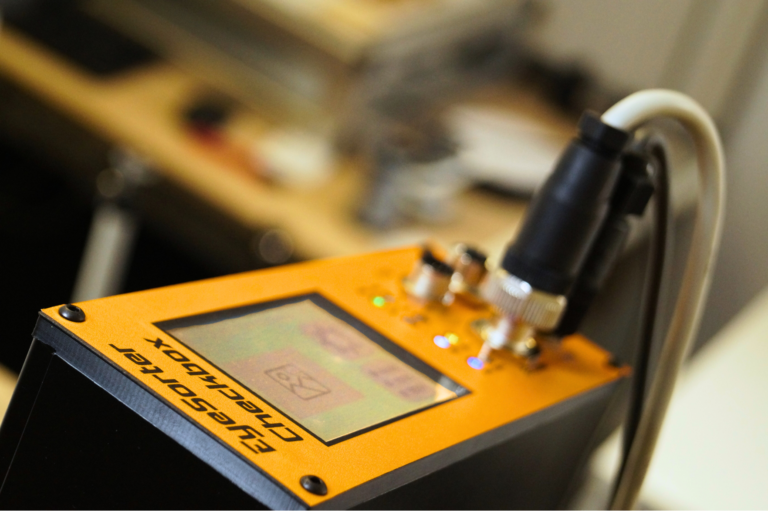
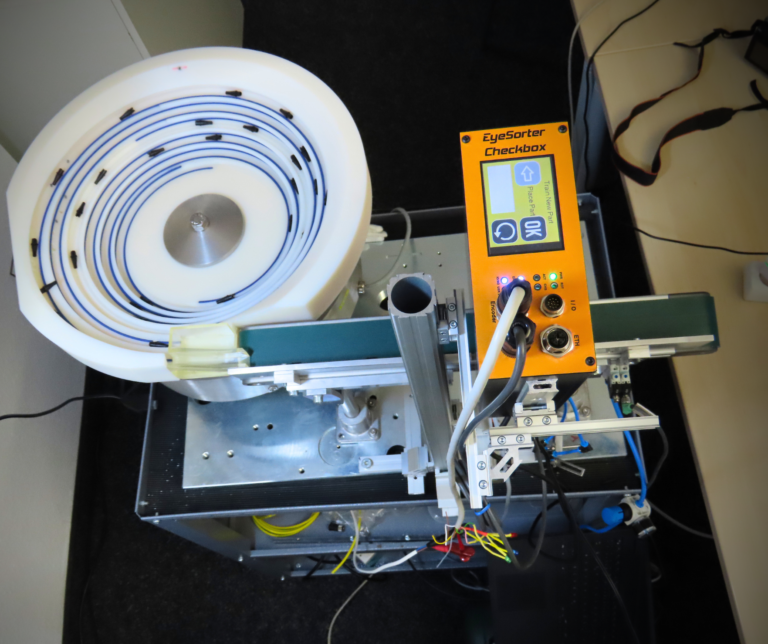
With the EyeSorter, EVT has developed a new product that is unparalleled in the field of industrial image processing.
In the production of small or medium-sized components in very large quantities, it is often necessary to check before further processing whether the component is transported to the next processing step without errors and in the correct position on the conveyor belt. For this application we have developed our EyeSorter. It consists of a compact unit and only needs to be mounted by the customer and parameterized to the component at the push of a button.
This is easily done via a touch monitor. After mechanical assembly, the worker teaches the system to a good part with a single push of a button and all subsequent components are checked for correctness and position. The result, with counter, is shown on the display and immediately made available via I/O interfaces, for example to control switches.
Direct monitoring & accurate sorting
The EyeSorter then sorts the parts based on the part contour data into:
- Direct overview of sorting
- Active part
- Total part counter
- Good part counter
- Bad part counter
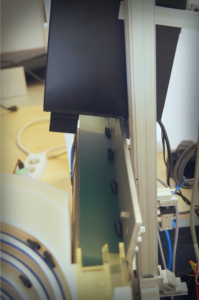
Single-Button-Training
Press Train Button > Feed Part > Start Sorting
Possible divider rates and speeds
Depending on the part layouts, part rates of 1500 and more per minute are achievable and part transport speeds of greater than 60 meters per minute.
Suitable parts
In principle, all workpieces that can be transported in a stable position and whose quality and positional orientation can be recognized by means of contour features in the camera image.
Color or material features can also be included in the inspection by means of additional sensors.
The main menu
- Start automatic process
- Train New Part
- Calibrate System
- Logfile
- System Info
- System Settings
- Control LED to indicate Power Good, Sort Active or Error
Simply touch to sort.
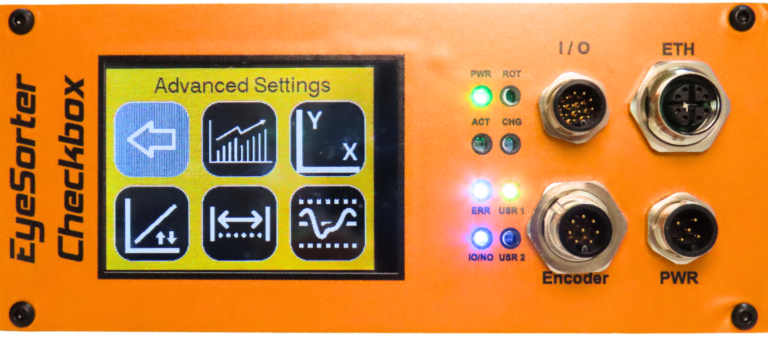
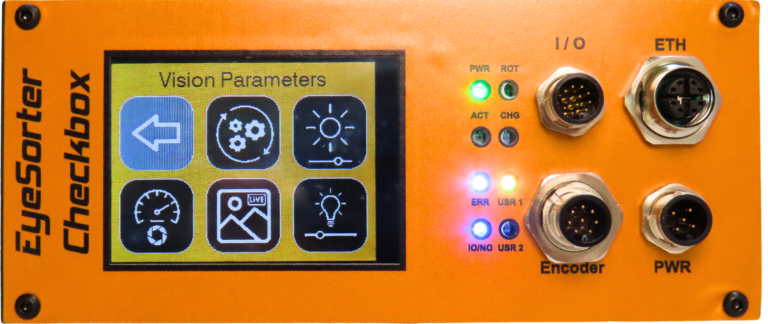
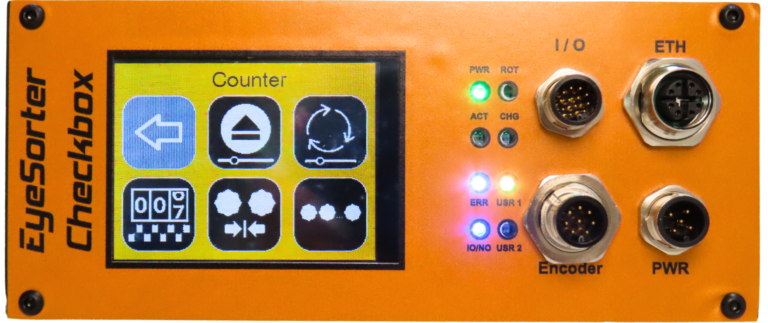
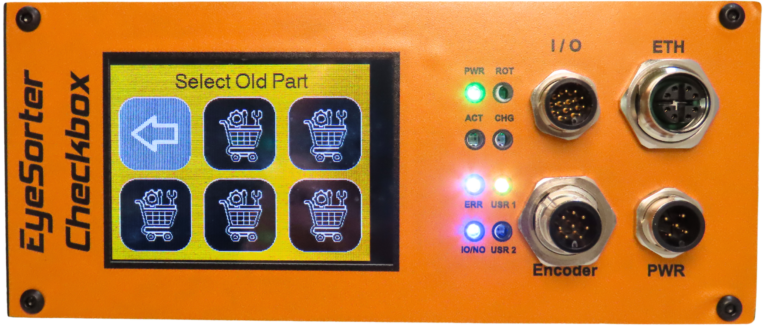
Machine Interface
- Encoder Connector
- Differential Interface 5 – 24 V
- A, B, Z Input for Encoder
- Power Connector 24 V, 2 A
- Ethernet Connector (Optional M12 GigE)
- Communication, Profinet, OPC UA, MQTT and more
System Ready > indicates System Ready for Sort
IO > indicates Good Part – activ with Encoder offset
NIO > as good part but not good
Rotate > as good part but control rotation needed
Waiting for Parts > No parts available – start feeder
Start- Stop Belt > Start- stop belt
Counter Exceed Max Count > Precount reached – change bucket
User Defined > e.g. Part Trigger
STL File
The STL file for fast system integration is available on request.
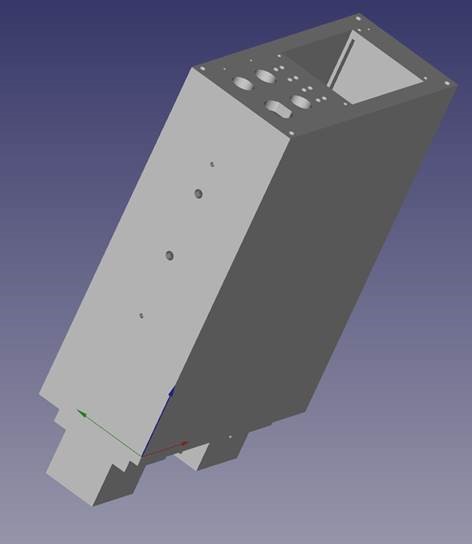